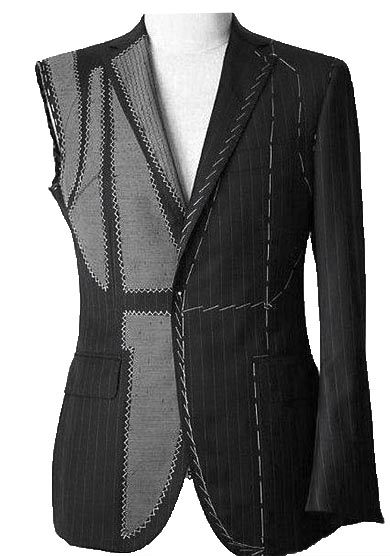
Interlining fabric definition
The interlining is based on woven fabrics, knitted fabrics and non-woven fabrics, using (or not using) thermoplastic polymer compounds, and is processed by special machinery for coating and finishing. Which is bonded (or non-bonded) with the fabric and play the rold of reinforcement, stiffening, support, stability and shape retention to the clothing.
The outside of a garment is the fabric, the inside is the lining, and the middle is the interlining, so in general, the interlining cannot be directly seen, but all the positions that need to be stiff, full, smooth transition, and reinforcement are all a interlining is required.
The main function of the interlining
Interlining is the skeleton of clothing, and good interlining is the essence of clothing, especially the application of modern interlining. Through the modeling, reinforcement and shape retention of interlining, clothing can form various beautiful styles, so that clothing modeling and sewing technology can be obtained. Unexpected effects, the role of the interlining can be roughly summarized into the following aspects:
1. Give the clothing a good curve and shape;
2. Enhance the stiffness and elasticity of clothing and enhance the three-dimensional sense;
3. Improve the drape and fabric feel of clothing and enhance the comfort of clothing;
4. Increase the thickness, plumpness and thermal insulation of clothing;
5. Prevent clothing from being deformed and keep the original shape after wearing and washing;
6. It can strengthen and reinforce some parts of the clothing.
Interlining production process
The production process of interlining is mainly divided into two types of production processes according to non-woven interlining and woven interlining.
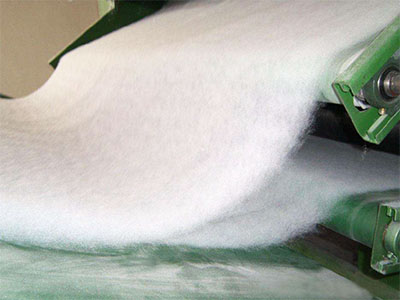
production process of non-woven interlining
Fiber dispersing – fiber laying – hot rolling or chemical bonding of fibers into cloth – coating – packaging & inspection

production process of woven interlining
Spinning–base fabric weaving — dyeing –setting–resin– drying –coating–packaging & inspection
Types of interlining
Interlinings are classified by production process and composition:
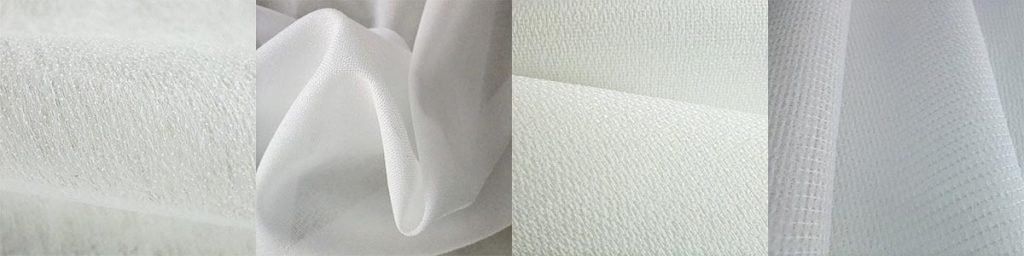
1. Chemical bonded non-woven interlining
Which is a kind of non-woven interlining. The non-woven base fabric is formed by immersing the fibers in chemical liquid, and then coating a layer of thermoplastic polymer compounds such as PA , PES, LDPE, EVA , etc.;
2. Thermal bond non-woven interlining
It is currently the most widely used non-woven interlining as its excellent performance, cost performance and chemical free. The base fabric of thermal bond non-woven interlining is produced by using heat to melt thermoplastic powders, the laid fiber layer is pressed by high-temperature hot rolling and the melt thermoplastic powders bond the fibers;
3. Cotton and linen interlining
Refers to the cotton or linen cloth that is not finished or only sizing and stiffened, which is a relatively primitive interlining;
4. Water jet woven interlining
Which is one kind of woven interlining but used water jet loom weaving cloth as base fabric, the material fibers composition normally is polyester, and yarn specification can be 30D, 50D until 300D, pain or twill weaving. Water jet woven interlining can do single dot or double dot coating with PA or PES glue according to requirements, which is widely used for, suit and women fashion clothes.
5. Warp-knitted interlining and warp-knitted brushed interlining
Generally use polyester or viscose as raw material, the base fabric is produced by warp knitting machine, and then bleaching or dyeing and other finishing, and uniformly coated with thermoplastic hot melt adhesive. lining. Specifically, it is divided into ordinary warp knitted interlining and brushed warp knitted interlining. Among them, the brushed warp knitted interlining has a thick feel and good toughness, and is mostly used in clothing such as suits and coats;
6. Four-sided elastic interlining
The knitted interlining has 4 ways stretch, good recovery performance and soft hand feeling, which makes up for the lack of elasticity of the woven interlining. The circular knitted fusible interlining is ideal for knitted garments with good elasticity;
7. Woven resin interlining
Cotton and chemical fiber pure spinning, blended woven or knitted cloth,, bleaching or dyeing and other finishing, and then do resin finishing to get stiffer hand feeling. Resin interlining is used for shirt collar, cuff, and cap brim;
8. Woven horse hair interlining
Also known as wool interlining, it is made of cotton, chemical fiber, wool pure spinning or blending as light yarn, chemical fiber and yak hair or other animal hair blending as weft yarn, warp weaving into base fabric, and resin finishing. made of interlining.
Interlinings are classified by clothing application and position:
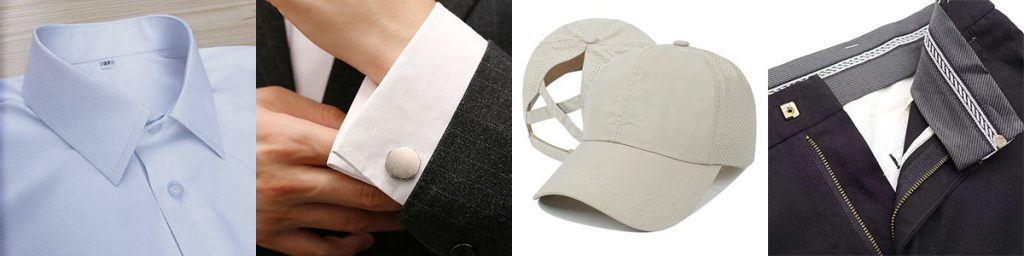
The parts used for the interlining are: the front piece, the inner welt, the collar, the lapel, the back piece, the pocket, the flap, the waistband, the collar, the placket, the cuff, the welt, the sleeve, the mouth, the hem fork Mouth, sleeve fork, etc.;
According to different clothing and position, it is divided into suit interlining, fashion interlining, shirt interlining, the Muslim robe interlining, hat interlining, trousers waistband interlining, collar interlining, etc.
Fusible interlining advantages
1. It can be firmly bonded to the fabric. After bonding, it feels soft, stiff, and resilient. After bonding, the surface of the fabric can recover quickly.
2. The bonding temperature is low, and the shrinkage is coordinated with the fabric.
3. The adhesive coating amount is uniform, the fixing amount is uniform, the adhesive has no leakage, anti-aging, and the long-term storage adhesion performance is also unchanged.
4. When cutting, the interlinings do not stick to each other, do not stick to cutting knives, non-stick sewing needles, and sewing machines, and the feeding is smooth.
5. Does not damage the physiology of clothing, such as breathability.
Using of fusible interlining
1. Bonding machine
There are generally two types of bonding machines: roller type and flat type.
2. Bonding conditions
Bonding conditions include bonding temperature, pressing time and pressure. In a certain range, the three elements interact with each other to a certain extent. When the temperature increases and the pressure increases, the pressing time can be relatively shortened, and vice versa. If the temperature is too high and the pressing time is too long, it is easy to damage the performance and color of the fabric, and it is also easy to produce glue penetration.
3. Selection of bonding conditions
Before mass production, the bonding conditions must be repeatedly tested to determine the optimal process conditions (when trying out small samples, the interlining supplier should provide bonding conditions for reference).
After the interlining is bonded to the fabric, peel it off. If the hot melt adhesive is evenly distributed on the interlining and the fabric, it means that the bonding conditions are appropriate, otherwise the test should be repeated. After bonding, the cloth surface should be flat, without wrinkles, bubbles, and glue. After bonding, the peel strength, dry cleaning and water washing performance tests should be carried out, and the test results should meet the production requirements. The effect of bonding should meet the style and characteristic requirements of clothing.